Environmentally-friendly materials in flexible packaging
Corrugated cardboard, kraft paper, bio-polymer... More and more environmentally-friendly materials are being used to dress up your products. More than just a trend, this is a real challenge for businesses. Environmentally-friendly design is now a major competitive advantage. Faced with environmental issues and consumers concerned about the future environmentally-friendly designed packaging is becoming a must. What is environmentally-friendly designed packaging? What environmentally-friendly materials are being used today to limit the impact on the environment? We've got the answers in this article. conçu devient un incontournable. Mais qu’est-ce qu’un emballage éco-conçu ? Quelles sont les matières éco-responsables utilisées aujourd’hui pour limiter l’impact sur l’environnement ? On vous répond dans cet article.What is environmentally-friendly designed packaging?
Packaging is the set of elements used to protect, transport, and present a product. But what makes it environmentally friendly?Environmentally-friendly designed packaging: the definition
Being environmentally responsible is an approach that incorporates environmental protection measures into its activities. By extension, environmentally-friendly designed packaging is packaging that limits its impact on the environment throughout its entire life cycle, i.e., from design to end-of-life, including transport and storage. To achieve this, there are a number of measures that can be taken to limit environmental impact: Reducing the weight of raw materials, local sourcing, consideration of recycling and end-of-life constraints, uniformity of packaging types to increase the recycling rate... All the stakeholders in the value chain have an impact on environmentally-friendly design through their actions.Recyclable packaging
Recyclable packaging is packaging that can be processed and reused again. It conserves natural resources by using the same material to create a new product. This reduces waste and environmental pollution. Many types of packaging can now be recycled, such as aluminium, cardboard, polymer, etc. A specific recycling logo can be found on the packaging, usually with arrows (depending on the material).
In the world of Flexible Packaging, the concept of recycling is as follows:
- Either the flexible packaging is made from a mono-polymer and will therefore be collected in the yellow bins: MonoPE, currently in France, and soon MonoPP.
- Either the packaging contains at least 51% cellulose fibre, so that it can be recycled in the paper industry: Paper composite
For the experts, there are subtleties and tolerances to manage the notions of barriers and the specificities of each project. That's why we can help you select the right materials for your packaging.
Polymer-free kraft packaging exists, but ...
The grail is undoubtedly packaging with a maximum of polymer-free fibres, and these solutions do exist. They are generally well suited to solid, dry products. In this field, these new materials can easily replace the complex multi-material films traditionally used. However, their application is fairly limited. Why? Because the thinness of the barrier and sealing layers makes it impossible to use them for wet products. Especially if you add the logistical constraints associated with e-commerce. Coatings, varnishes, or lacquers systematically provide a sealing function and a barrier function, but they are rarely combined with others (grease, humidity, O2, etc.). But innovations are advancing so fast that, at the time of writing, there may already be something new. These structures generally have a fibre content of over 85%.
But what solutions are there for a wet product?
In the still numerous cases where the solutions already mentioned cannot be applied, we can offer papers combined with polymer films that will provide the functions that paper alone, or varnished paper, do not have: Barrier or high barrier and mechanical resistance essentially. The fibre content of these structures ranges from 51% to 80%, depending on the application.
However, the addition of accessories (spouts, zips, etc.) tends to reduce the fibre content. This is why we are developing concepts and solutions to eliminate these accessories without compromising the user experience.
Metallized paper composite
Laminating paper and metal is common in packaging. This is a way of providing protection that paper alone cannot guarantee. Aluminium, for example, is widely used in the food and pharmaceutical industries for its barrier properties. It is a light, recyclable material that can be combined with yoghurt lids and food cartons, for example.
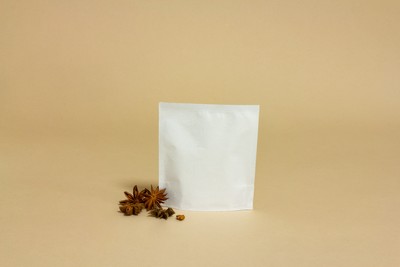
Composite kraft paper
Resistant and biodegradable, kraft paper is the king of packaging. It is used both to store products and to pad boxes to stabilise goods. You can find it laid (natural look), glazed (with a glossy side), creped (elastic) or 100% recyclable.
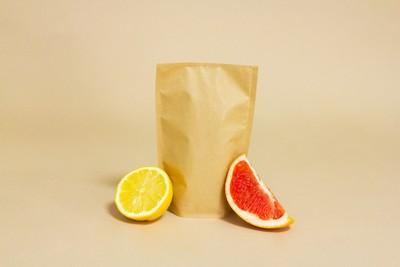
Apple paper composite
The world of packaging is constantly evolving. You'll find more and more innovations and environmentally responsible materials on the market for packaging your products. How about an apple paper composite, made from 15% recycled apple fibre? It's an original and 100% healthy idea that's sure to put you in the spotlight! Sealester offers this exclusive service for your food products. .
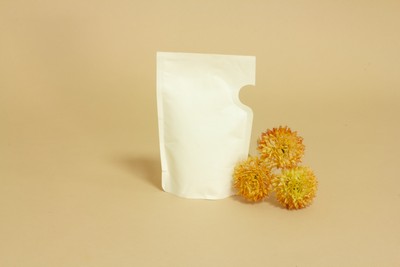
Coated composite
This composite, made up of 85% fibre, significantly reduces polymer waste and allows packaging to be fully recyclable in the paper industry. This innovation is still limited to non-wet products, but it is gradually developing new barriers to enable brands to meet the new expectations of consumers and the planet.
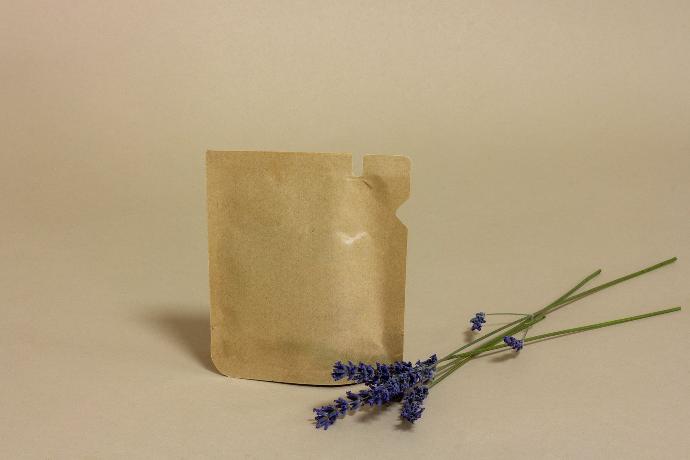
Mono-polymer packaging
Polymers are still widely used in the world of flexible packaging. In the face of environmental challenges, they are at the centre of discussions. However, they can be recycled and recyclable - in other words, they can become a sustainable material in the same way as cardboard. This is the case with mono-polymer packaging.

What is mono-polymer packaging?
As its name suggests, mono-polymer packaging is made from just one type of polymer. It has the versatility, strength, and impermeability of polymer, while being easier to recycle after use. Mono-polymer packaging therefore contributes to the circular economy, unlike multi-material packaging, which sometimes poses problems at recycling centres.
In France today, only monoPE packaging is collected and recycled in sorting facilities. Organisations are currently working on a flexible MonoPP sorting system, but this is not yet considered recyclable in France.
Mono-PE material
Do you want to take advantage of the benefits of a polymer to preserve your products? Choose a thermoplastic that reversibly melts at a certain temperature, such as PE. This is an environmentally responsible material which, at the end of its life, is transformed into granules to be reused in the manufacture of new packaging. For example, Doypack-type polymer pouches are made from mono-PE (polyethylene), because it is a highly versatile, moisture-resistant polymer. It is even possible to incorporate a very thin layer of EVOH material into the PE to reinforce the oxygen barrier properties, without affecting the recyclability of the packaging.
In the MonoPE family, we work with 2 types of structure:
On the one hand, there are Coextruded Films, where all the functions have been added to the film during manufacture: Sealability, barrier, mechanical strength, printability. These films can be printed on the surface, saving on lamination operations. Please note that, once again, this solution is not applicable to all projects. Our teams of experts are here to guide you in your choices.
There are also MonoPE laminates: A PE film with printing and mechanical properties is bonded to a thicker film that also provides mechanical properties and sealability (see laminating article). These film structures are the most common in the MonoPE family.